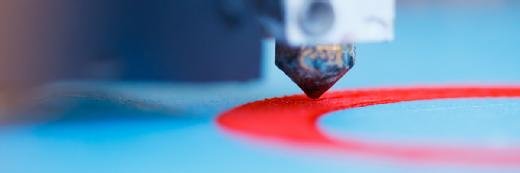
nikkytok - Fotolia
How 3D printing will disrupt industry worldwide
The technology is helping startups model prototypes and inventory suppliers lop millions from supply chain costs
The market for 3D printing is worth $5bn now, but it is predicted to grow eightfold in the next four years – and most of that growth will be in the enterprise and industrial markets. That’s according to analysts who see huge potential in the technology – but what will it offer CIOs?
“Right now, the technology is at the sweet spot of the adoption curve,” says Tasha Keeney, an industrial innovation analyst at New York-based Ark Invest. The investment firm finds early market opportunities, and has chosen 3D printing as one of its focus industries, producing an exchange-traded fund to help investors interested in the sector.
Keeney has good reason to predict a $40bn market by 2020. The 3D printing sector has been depressed by poor performance on the consumer side, while the poor dollar has hurt sales to the industrial sector, she believes.
These are transitory market conditions, though, whereas she thinks the advantage of 3D printing is permanent: complexity is free. It is possible to print single parts that wouldn’t be viable with traditional techniques such as injection moulding.
“GE used 3D printing to create a fuel nozzle for its Leap engine. The part used to be 18 parts but, with 3D printing, they can do it in one,” she says. “That makes it much stronger. In other cases, if you’re able to switch materials, you can save on cost but also on weight, which is important in areas like aerospace.”
An evolving technology
3D printing technology has been around in the industrial sector for several years, but the technology garnered mainstream attention when the hobbyist/maker 3D printing market took off. That was powered by fused deposition modelling (FDM) technology, which uses a heated nozzle to print material in layers, building up an object over time. The detail on the object is typically imperfect because of the difficulty of putting layers precisely on top of each other.
Next up the price scale are stereolithography and digital light processing (SLA and DLP), which use a liquid resin photopolymer cured by light. Whereas FDM is suitable for low-cost prototypes, these two methods, with their high level of detail, lend themselves to more intricate prototypes. SLA made its way into the prosumer market (goods of a standard between those aimed at consumers and professionals) via companies such as Formlabs, which focuses on clients such as startups, who want to use it for prototyping or custom short-run manufacturing.
Startups will use this to refine their products in the early stages before investing in costly injection moulding techniques, explains Michael Sorkin, European general manager at Formlabs.
“This is a more efficient way of changing the product in the beginning. Startups are using this more at the beginning than later on,” he says.
At the mid- to high-end, you’ll find selective laser sintering, which uses lasers to heat powdered material (typically nylon), turning it into a solid. This technology is useful for complex designs. Even more sophisticated material jetting technology is used for highly detailed, realistic prototypes.
The product lifecycle
Although prototyping still makes up the bulk of his employer’s revenue, the applications for 3D printing are expanding, according to Josh Claman, chief business officer at Stratesys, a high-end firm that specialises in material jetting.
The most promising short-to mid-term market after prototyping is production tooling, Claman says. “These are jigs and fixtures and tools that help increase the productivity or improve the safety or velocity of the manufacturing tools,” he says. These have traditionally been expensive devices with long production lead times of their own. These are now printable and potentially even customisable for specific workers, he explains.
A longer-term and far bigger opportunity lies in production parts, Claman adds. Adoption at the moment is barely out of the experimental stages, but it is particularly relevant in industries with short-run production of highly complex parts, such as aerospace. Stratesys is currently working with Airbus to print parts for the A350 aircraft.
There are nuances to the production parts application, though, particularly in the area of after-market parts. Product lifecyle management is a huge logistical task for many companies, who must make the appropriate inventory available at the right time.
“If you’re a capital equipment company and the equipment lasts a long time, you might have to hold $500m in inventory across the world,” he says. “The carrying cost of that, the logistical overhead, is enormous.”
Being able to print components on the fly eliminates that problem, creating opportunities to service parts that break often, decreasing service times and making the supply chain nimbler. Stratesys is already conducting pilots with some companies who are weighing up the cost of 3D printing versus traditional moulding techniques for the production and after-sales parts market.
Startup disruptors
Read more about 3D printing
HP Inc rolls out its first 3D printer, with hopes that it will revolutionise manufacturing.
Samsung has established an advanced technology team in its mobile division as it looks to invest in future areas of growth
For many smaller companies, the multi-thousand dollar printers to create this kind of product are out of reach – for which there are companies marketing 3D printing as a service, to drive disruption in their clients’ industries.
Shapeways, a spin-off from Royal Philips Electronics in the Netherlands, has a range of high-end printers at its facilities in Long Island New York and Eindhoven. Its software allows any user to upload a CAD drawing and have it printed in any of 60 materials, including metals.
Lauren Slowik, design evangelist for Shapeways, says this removes the normal economies of scale of manufacturing services, making the per-unit cost the same for one or many units.
“Because the complexities are managed by the software element rather than creating a mould for injection moulding or having a skilled machinist do the tooling, all the skilled elements of the manufacturing are contained in the precision of the machine or the file you’re submitting,” she says.
The company uses industrial-capacity machines that can print many different objects simultaneously, making the cost of printing merely a function of machine space and material, she says. “Our area of innovation is in the profit model.”
The limits of materials science
Shapeways machines’ metal printing uses selective laser melting technology. In the right hands, printing processes such as these enable companies to create limited runs of highly engineered aerospace and automotive parts. Even with the many materials on hand, though, the barriers to entry for some specialised production applications are high.
There are some 3D parts for heavily regulated industries – such as aerospace – that must be certified in a process that can take years. This process can involving stress testing, X-rays, and analysis of toxicity and flammability to precise thresholds, says Stratesys’ Claman. Some parts simply can’t be printed yet because of the current limitations in materials science.
This is changing, though. Keeney points to new materials and printing processes that can have produce different colours and tensile properties in the same printed unit, so that a single part could be flexible and red in one area, and rigid and yellow in another, for example.
The future is on the printer
HP Inc – which recently launched a selection of relatively low-cost industrial printers using its own multi-jet fusion technology – has its own open marketplace for materials, allowing suppliers to innovate with different options.
The company is also working on printing processes and materials that have different colour layers, explains its worldwide marketing director for 3D printing, Alex Monino.
“You can print on the part a layer of colour below the black, so you can track the wear and tear of the part,” he says.
Also in the labs are parts with conductive properties, which would enable printers to embed LED indicators and other circuitry directly into printed components, he says. This would enable printed components to be ready for the internet of things. “Every plastic part of an airplane could in the future be able to report its stress and thermal condition,” says Monino.
HP is not the only company innovating in the 3D printing space. Ark’s Keeney points to Carbon 3D, an organisation still in startup mode that creates high-quality parts at relatively low cost, which she says is going after the short-run manufacturing market for niche automobiles.
“It’s certainly going to take the low-volume, more customised end of things which is actually where we see manufacturers going. Manufacturers want to have more adaptable processes.”
Within half a decade, 3D printing could disrupt the product management and supply cycles for some companies just as heavily as it has disrupted their prototyping process today.
The future is being printed as we speak.